윤활이란?
윤활의 목적은 상대운동을 하는 물체를 전단력이 적은 윤활막에 의하여 분리시킴으로써 표면의 손상을 방지하는 것이다. 윤활막 두께와 표면의 조도에 따라 유체윤활, 혼합윤활, 경계윤활로 분류할 수 있다
윤활의 형태: 윤활은 윤활제와 미끄럼 표면과의 분리된 정도에 따라 보통 다음과 같이 분류되며 다음 그림은 이 경우들을 개념적으로 보여 준다.
유체윤활
(Hydrodynamic Lubrication)
유체윤활은 접촉면이 윤활제에 의하여 완전히 분리된 경우를 말한다. 이 경우에 접촉표면에 걸리는 하중은 모두 접촉면의 상대운동에 의해 발생되어지는 유압에 의하여 지지되게 된다. 따라서 접촉 표면이 마모는 매우 작으며 마찰 손실도 오직 윤활막 내에서 이루어지게 된다. 유체윤활시의 최소 유막두
께는 0.008 - 0.020 mm 정도이며 마찰계수는 0.002 - 0.01 범위이다.
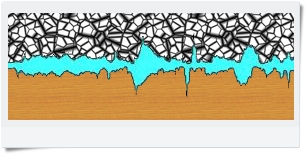
혼합윤활
(Mixed-film Lubrication)
혼합윤활은 접촉표면의 돌기들의 간헐적인 접촉과 부분적인 유체윤활이 혼합되어 있는 윤활을 말한다. 이때 마찰 계수는 0.004 - 0.10 정도의 범위에 있고 접촉 표면의 약간의 마모도 수반하게 된다.
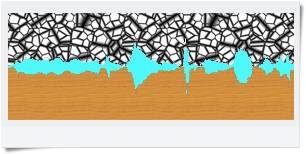
경계윤활
(boundary Lubrication)
경계 윤활은 그림에서 보는 바와 같이 계속적이고 심한 표면 접촉이 일어나면서도 유활유는 접촉 표면에 계속하여 공급되어서 접촉표면에 마찰과 마모를 감소시킬 수 있는 표면막을 형성하는 윤활을 말한다. 이경우 마찰계수는 보통 0.05 - 0.20 범위에 있다
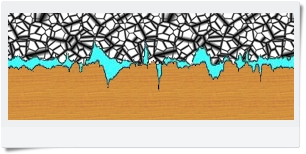
Stribeck Curve
윤활형태에 영향을 미치는 기본변수들을 살펴보기 위하여 저어널베어링의 예를 생각해 보기로 하자 그림은 저어널베어링에서의 세가지 변수들과 마찰계수와의 관계를 보여주는데 이것을 Stribeck Curve라고 한다. 여기서 가로축의 ηN/P 를 베어링 특성치라고 하며 이들은 점도(η), 축의 회전수 (N), 그리고 축의 단위면적당 압력 (P)으로 구성되어 있다.
이러한 변수들이 윤활형태에 미치는 영향을 살펴보면 다음과 같다.
점도 (Viscosity)
점도가 높을수록 주어진 부하에서 유체윤활을 이루기 위한 회전속도는 낮아진다. 유체윤활을 이루기 위하여 필요한 점도보다 높은 점도는 축의 회전시 오일막을 전단하는데 필요한 힘을 증가시키므로 마찰을 증가시킨다.
회전 속도 (Rotation speed)
회전속도가 빠를수록 유체윤활을 이루기 위한 윤활유의 점도는 낮아진다. 그러나 일단 유체윤활이 이루어지면 회전속도의 증가는 축의 회전시 오일막을 전단하는 일의 증가를 수반하므로 마찰을 증가시킨다.
단위면적당부하
(Bearing Unit Load)
단위 면적당의 부하가 작으면 작을수록 유체윤활을 이루기 위하여 필요한 회전속도와 점도도 낮아진다. 그러나 오일막을 전단하는데는 어떤 힘이 필요하므로 부하를 계속줄인다고 하여서 그 만큼 마찰력이 줄어드는 것은 아니다. 따라서 마찰계수는 증가한다.
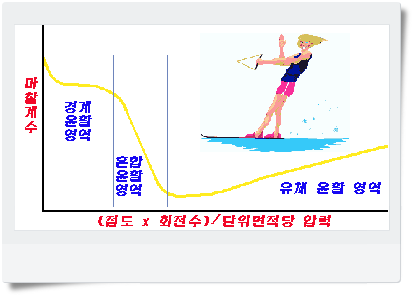
윤활제의 종류
윤활제는 액체, 반고체, 고체, 그리고 기체로 나누어지며 그 사용장소, 사용방법, 마찰의 종류등에 의하여 적당한 것을 채용한다.
액체 윤활유
과거에는 주로 동식물성 윤활유가 사용되어 왔으나 최근 석유공업의 발전에 따라서 석유원유에서 양질의 윤활유를 제조할 수 있도록 되었고 오늘날에 와서는 광물성 윤활유가 윤활유 전체를 거의 차지한다고 하여도 과언이 아니다.
반고체 윤활제
주로 그리스류를 말하며 윤활을 하는데 힘이 들지 않고 접근이 어려운 곳에 한번 주입함으로 오래 사용할 수 있는 장점이 있어서 널리 사용되고 있다. 고체 윤활제는 흑연, 이황화몰리브덴, PTFE등이 있으며 윤활성이 액체 윤활제보다 온도에 덜 민감한 장점이 있다.
고체 및 기체 윤활
넓은 온도범위 약 (-200 ~ 2000도)에서 쓰일 수 있는 장점이 있다. 열팽창과 마모 문제 때문에 이와 같은 고온에서 사용할 수 있는 액체나 반고체 윤활시스템을 설계하기는 현실적으로 매우 힘들다. 일반적으로 넓은 온도 범위에서 사용되는 윤활제로서, 낮은 속도와 높은 부하에서는 고체 윤활제를 그리고 높은 속도와 낮은 부하에서는 기체 윤활제를 사용한다.
윤활형태별 마찰계수
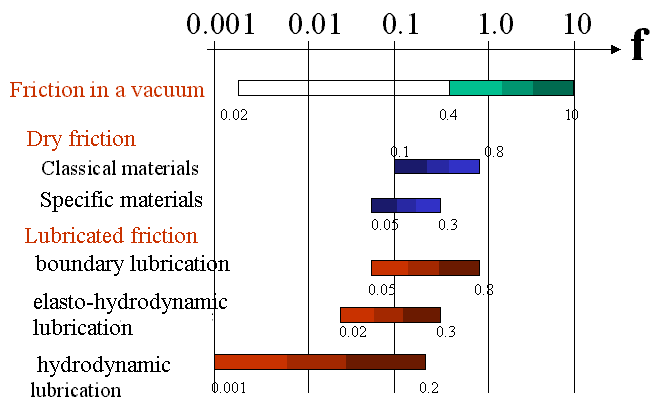